
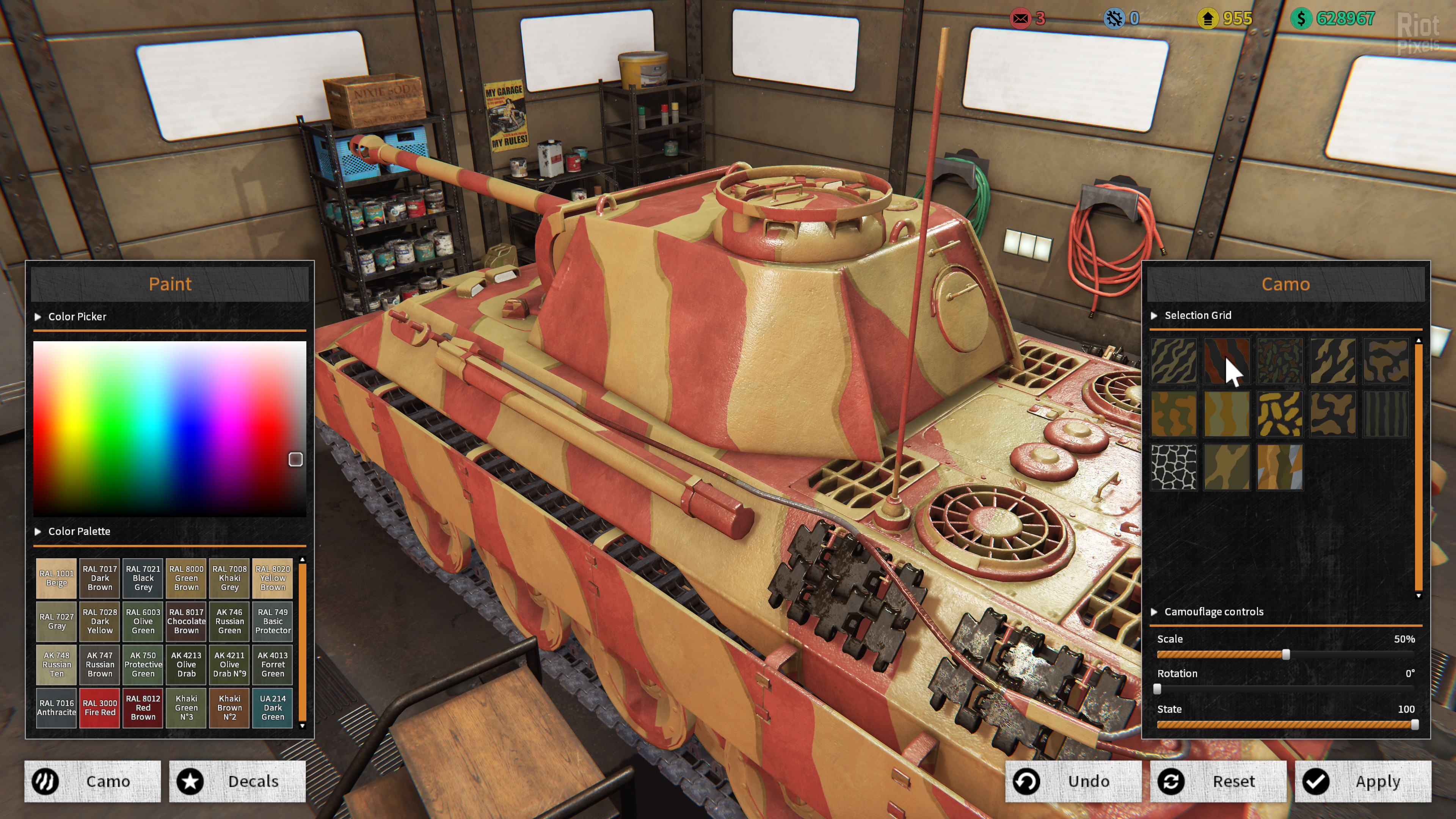
ZADGHAFFARI R, MOGHADDAS J S, REVSTEDT J. Mixing times in a turbulent stirred tank by means of LES. HARTMANN H, DERKSEN J J, HEA VAN DEN AKKER. Chinese Journal Chemical Engineerig, 2006, 14(1): 1–7. Large eddy simulation of mixing time in a stirred tank. Large eddy simulation of the turbulent flow in a stirred reactor. Transactions of the institution of Chemical Engineers Research and Design, 2000, 78(3): 327–333. CFD study of homogenization with dual Rushton turbines-comparison with experimental results. The use of compuational fluid dynamic (CFD) to estimate mixing times in a stirred tank. A liquid crystal thermographic technique for the measurement of mixing characteristics in stirred vessel. Mixing time analysis using colorimetric method and image processing. (in Chinese)ĬABARET F, BONNOT S, FRADETTE L. Journal of Chemical Engineering of Chinese Universities, 2000, 14(4): 328–333. Mixing time in stirred tank of three phase gas-liquid-floating particle systems. Effect of impeller design on liquid phase mixing in mechanically agitated reactors. Liquidphase mixing times in sparged and boiling agitated reactors with high gas loading. ZHAO D, GAO Z, MULLER-STEINHAGEN H, et al. Chemical Engineering Communications, 1988, 74(1): 1–25. Liquid phase mixing in mechanically agitated vessels.
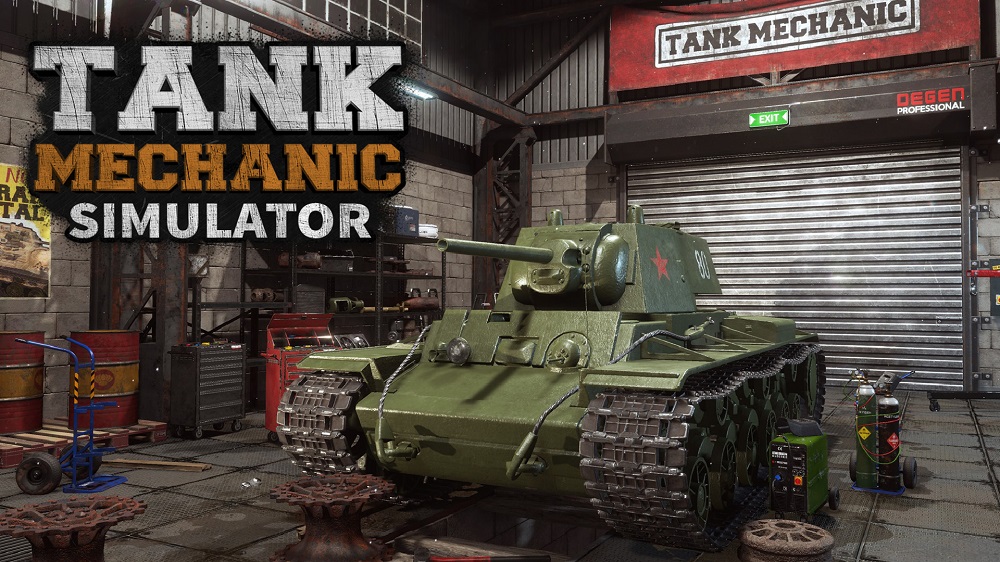
The research presents helpful references for design, optimization and scale-up of agitated tanks with multi-impeller.īIGGS R D. The global mixing time is the shortest for the merging flow, followed by diverging flow, and the longest for parallel flow. Parallel, merging and diverging flow pattern form in the agitated tank, respectively, by changing the impeller spacing and clearance of lower impeller from the bottom of the tank. Dimensionless global mixing time remains unchanged with increasing of impeller speed. Two methods are used to determine global mixing time and get close result. Mixing efficiency is the highest for the feeding point at location of midway of the two impellers. The simulated results show that feeding points have great influence on mixing process and mixing time. Local and global mixing time in the agitated tank is predicted by solving a tracer concentration scalar transport equation. The simulation results indicate that the DES method can obtain more flow details than Reynolds-averaged Navier-Stokes(RANS) model. The simulated flow patterns and liquid velocities in the agitated tank are verified by experimental data in the literature. A sliding mesh(SM) approach is adopted to solve the rotation of the impeller.
#TANK MECHANIC SIMULATOR FEEDBACK SOFTWARE#
On the basis of computational fluid dynamics(CFD) software package Fluent 6.2, the mixing characteristics in a tank agitated by dual six-blade-Rushton-turbines(6-DT) are predicted using the detached eddy simulation(DES) method. The turbulence model is very critical to predicting mixing process in agitated tanks. The Issue of mixing efficiency in agitated tanks has drawn serious concern in many industrial processes.
